موضوع مورد بحث این مقاله این است که ساخت فولاد در ایران از چه زمان آغاز شد و در حال حاضر وضعیت تولید فولاد در ایران و نقش کشورمان در بازار فولاد جهان در چه جایگاهی قرار دارد؟ این نکات برای مدیران و کسانی که در صنایع فولاد فعالیت دارند اهمیت بسزایی دارد.
همانطور که می دانیم نیاکان ما از زمان عصر آهن از پیشروان صنعت فولاد بوده اند. در دوران قبل از میلاد, بشر با کشف آهن شروع به ساختن انواع چاقوهای شکار و سرنیزه و زیور آلات و سایر وسایل مورد نیاز خود کرد. همچنین در حکومت های مختلف پارسی در این سرزمین صنعت فولاد را با دانش روز آن زمان دنبال می کردند.
ولی بعد از رویداد انقلاب صنعتی و پیشرفت های چشمگیر غرب و بعضی از کشورهای شرقی, کشورهای زیادی برای تولید فولاد از یکدیگر سبقت گرفتند و با گذشت زمان انواع کارخانه های تولید محصولات فولادی پدید آمد.
حال اگر بخواهیم تاریخچه فولاد در ایران را بررسی کنیم لازم است بدانیم که تولید فولاد در ایران از سال 1306 آغاز شد.
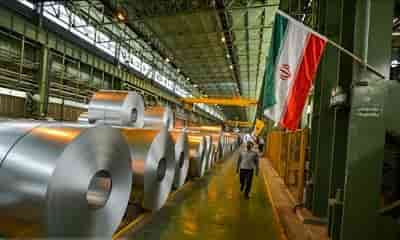
تولید فولاد در ایران
در سال 1306 حکومت وقت ایران برای تامین نیازهای ریل های آهن کشور تلاش های بسیاری انجام داد که می توانیم بگوییم آغاز کار فولاد در کشور در این تاریخ شروع شده است. به عبارتی میتوان گفت که تاریخچه فولاد در ایران به این تاریخ برمیگردد ولی به طور دقیق و حرفه ای تر زمان آن را در ادامه بررسی می کنیم.
حکومت وقت در آن دوره زمانی به دلیل فوریتی که برای احداث ریل آهن داشت بودجهی 5.5 میلیون تومان را برای این پروژه در نظر گرفت که راه اندازی اولیه این پروژه موفقیت آمیز بود ولی مشکلات مالی که تا سال 1328 به وجود آمد دلیلی برای آن شد تا پروژه به تاخیر بیفتد.
در سال 1328 بعد از کودتای 28 مرداد قراردادی به نام کنسرسیوم بین آلمان و ایران منعقد شد و بعد از آن پروژهی راه اندازی فولاد دوباره رونق گرفت. با توجه به مدارکی که از آن زمان در دسترس است می توانیم بگوییم به طور جدی تاریخچه ی فولاد کارخانه ای در ایران از این سال شروع شده است.
کنسرسیوم آلمان برنامه ریزی ای انجام داد تا کارحانه تولید فولاد بتواند روزانه 150 تن فولاد را تولید کند. در آن زمان آلمان دستگاه های نورد را برای احداث کارخانجات جدید به ایران منتقل کرد و 1200 نفر نیروی انسانی در آن سال ها به فعالیت مشغول شدند.
مشکلاتی که باعث کند شدن روند رشد در آن سالها شد
در سال 1941 و در طول جنگ جهانی دوم هنگامی که جبههی استالین شکست خورد و ایران به وسیلهی نیروهای متفقین مورد تصرف قرار گرفت, آلمان خاک ایران را ترک کرد و بعد از آن پروژهی تولید فولاد همچنان به تعویق افتاد.
در آن زمان کارخانه تولید فولاد در کرج (که اکنون در کرج، بلوار ذوب آهن قرار دارد و در تاریخ 1329 تاسیس شده) احداث شده بود که شرایط بحرانی جنگ هر چه را که ساخته شده بود به ویرانه تبدیل کرد و تمام دستگاهها و تجهیزات را متفقین به تصرف خود در آوردند.
بعد از پایان جنگ جهانی دوم بودجه لازم برای آغاز دوباره تولید فولاد در کشور در دسترس نبود بنابراین پروژه های فولادی با شکست مواجه شدند اما کارخانه ها طرح هایی را برای آغاز به کار فولاد ارائه کردند ولی بانک جهانی سرمایه ای را به کارخانه ها اختصاص نداد.
همچنان راه اندازی پروژهی فولاد در ایران به تعویق می افتاد تا آنجا که دولت وقت ایران در سال 1342 با متخصصین سوئد همکاری هایی را شکل داد و تولید فولاد را با افتتاح کارخانه ای با تجهیزات کامل راه اندازی کرد و تولیدات اولیه آن برای مصارف نیازهای ارتش و راه آهن و خودروسازی داخل اختصاص پیدا کرد. بالاخره ایران توانست این رویا را به حقیقت تبدیل کند.
سرانجام در سال 1344 اصلی ترین کارخانه فولاد ایران در اصفهان پایه گذاری شد و بودجه و سرمایهی اولیه آن با صادرات گاز طبیعی به روسیه محیا شد. فولاد آریامهر در اصفهان سالانه 550 هزار تن تولید فولاد در ایران را بر عهده گرفت.
با توجه به شواهد و آمارها تولید فولاد در ایران تا سال 1383 بیشترین سقف تولید سالانه را داشته است ولی تحریم ها و مسائل سیاسی جزو بیشترین مسائلی بودند که تولید فولاد را در ایران دچار مشکل کردند.
تولید فولاد در ایران بعد از جنگ جهانی دوم
در سال 1960 برای اولین بار ایران (در اهواز) به تولید چدن پرداخت تا نیازهای خود را در خودروسازی برآورده سازد. محصول اصلی آن لوله های چدنی بود تا بتوانند سالانه بیش تر از 6 هزار تن تولید فولاد را افزایش دهند.
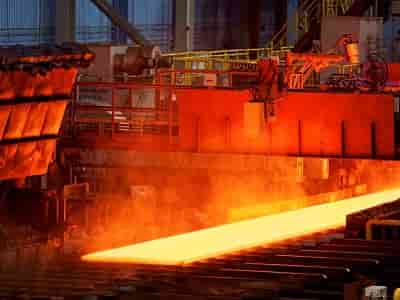
تولید فولاد در ایران در دهه 90
تولید فولاد در ایران تا سال 83 با بیشتری رشد خود به سقف تولید سالانه 12 میلیون تن رسید. اما تحریم ها و مشکلات سیاسی باعث شد که تولید فولاد در ایران افت شدیدی داشته باشد.
تحریم هایی که علیه ایران بود تا اواخر دهه 80 شمسی موجب شد با توجه به نیازهای زیاد به استیل و فولاد کربن, آنها را وارد کنند تا اینکه با مقاومت اقتصادی کشور و ایجاد تولیدی های جدید, ایران نه تنها نیازهای اصلی فولاد را خود تامین کرد بلکه در سال 1398 توانستیم به صادرات فولاد نیز دست پیدا کنیم.
فولاد چیست؟ و چه نیازی به تولید آن است؟
فولاد یا پولاد آلیاژی از آهن است که به طور تقریبی 002/0 تا ½ درصد از وزن آن را کربن تشکیل می دهد.خواص فولاد با تغییر در درصد کربن آن، عناصر آلیاژی و عملیات حرارتی قابل تغییر است.
استفاده از فولاد به دلیل استحکام, کشش نهایی و قیمت نسبتا پایین آن در ساختن صنایع مختلف مثل سازههای زیر ساختی، ابزارها، کشتیها، قطارها، ماشین آلات و خودرو ها بسیار کاربرد دارد.
در حال حاضر برای تولید فولاد از روشهای جدیدی مثل فولادسازی به روش اکسیژن قلیایی مورد استفاده قرار می گیرد. در روش اکسیژن قلیایی علاوه بر اینکه قیمت ها کاهش پیدا می کند باعث افزایش خلوص فولاد تولیدی هم می شود.
فولاد یکی از بیشترین محصولات تولید شده به وسیله انسان است و سالانه به طور تقریبی بیش از ۱٫۶ میلیارد تن فولاد در سرتاسر جهان تولید میشود.
ساخت فولاد
برای ساختن فولاد دو روش مهم وجود دارد:
- روش اول با استفاده از آهن اسفنجی و کوره های قوس الکتریکی برای ذوب آهن اسفنجی و سپس آلیاژسازی استفاده می شود.
- روش دوم استفاده از آهن خام (آهنی که تولید می شود در فرآیند احیای غیرمستقیم است) و سوزاندن کربن اضافی آن است.
طی این فرآیند میزان کربن آهن خام از بازهٔ ۵٫۳ تا ۶ به ۲٫۰ تا ۱٫۵ درصد وزنی کاهش مییابد. سپس عناصر دیگر در آن افزوده میشوند تا ترکیب موردنظر به دست آید.
آهن اغلب به صورت سنگ های معدنی مثل مگنتیت و هماتیت که در پوسته زمین هستند پیدا می شود. در فولاد سازی فولاد را با سوراندن کربن اضافی آهن خام سفید و بعد هم جوش کردن آن با مقدار کمی کربن و میزان کردن عناصر دیگر در آن با دو روش ذوب کردن و خمیر کردن تولید می کنند.
تولید فولاد به روش خمیری
در ابتدای صنعت فولادسازی تولید فولاد به این روش انجام می شد.
در تولید فولاد به روش خمیری, آهن خام را درون تشت کوره شعله می گذارند و آن را در برابر حرارت بسیار زیاد قرار می دهند تا آهن ذوب شود. سپس آهنی را که ذوب کرده اند به هم میزنند تا کربن موجود در آن در تماس با هوا بسوزد.
بعد از آن که کربن موجود در آن به مقدار زیادی در حالت دی اکسید کربن از ماده مذاب جدا شد دمای ذوب آن بالا رفته و به حالت خمیری در می آید. خمیرهای فولادی را با گاز انبر به صورت قطعه قطعه از کوره در می آورند و با پتک بر روی آن کوبیده می شود تا سرباره ای که در آن تشکیل شده بود جدا شود و به صورت یکپارچه در بیاید و بعد مورد استفاده قرار می گیرد.
روش خمیری چون ظرفیت تولید کافی ندارد و فولاد به دست آمده از این روش کیفیت یکسانی ندارد دیگر مورد استفاده قرار نمی گیرد.
تولید فولاد به روش ذوبی
در حال حاضر به طور تقریبی کلیهی فولادی که در جهان تولید می شود از طریق ذوب آهن به روشهای متفاوت به دست میآید که این روشها میتوانند به وسیله فولادسازی در کنورتور یا کوره های قوس الکتریکی انجام شود.
در این روش (کنوروتور)، آهنخامی که از فرآیند کوره بلند ذوب شده است را درون کنورتور می ریزند و با استفاده از دمیدن گاز اکسیژن در آن کربن های اضافی ماده مذاب سوخته می شود که بعد از انجام این مرحلهی مهم کربنی که در فولاد است به میزان دلخواه می رسد و بعد از آن عناصری از آلیاژهای مختلف را به آن اضافه میکنند تا استحکام فولاد زیاد شود.
در روش تولید فولاد به وسیله کوره های قوس الکتریکی در اولین اقدام آهن اسفنجی تولید شده را با فرآیند احیای مستقیم درون کوره های قوس الکتریکی میریزند تا حالت مذاب بگیرد. قابل توجه است که دما درون این کوره ها به اندازه ای است که در همان ابتدای فرآیند ذوب شدن فولادی با درصد کربن تقریبا پایینی تولید می شود. در دومین مرحله فولادی که تولید شده است را درون کوره های پاتیلی می ریزند تا در آنجا بر روی آنها عملیات آلیاژسازی انجام شود.
این مرحله شامل تنظیم مقدار کربن موجود در آن و اضافه کردن عنصرهای آلیاژی و یکدست کردن ترکیبات فولاد است. در انتها بعد از به وجود آمدن ترکیب شیمیایی مورد نظر, در صورت لزوم آن را به قسمت ریخته گری می برند و در بیشتر اوقات فولاد ریخته گری مداوم می شود مثل تختال و تیرآهن و میلگرد.
در مورد عناصر آلیاژی چه می دانید؟
عنصر کربن | باعث می شود مقاومت فولاد نسبت به سایش افزایش پیدا کند. |
عنصر منگنز | باعث افزایش قابلیت سختکاری عمیق تر می شود. |
سیلیسیم | استحکام فولاد را افزایش می دهد. |
کروم | باعث زیاد شدن مقاومت فولاد نسبت به سایش می شود. |
نیکل | باعث مقاومت تقریبی کم نسبت به سایش می شود. |
تنکستن | باعث می شود مقاومت فولاد به سایش افزایش پیدا کند. |
وانادیم | باعث کوچک تر شدن میکرو ساختارها می شود. |
مولبیدن | باعث می شود فولاد نسبت به گرما مقاومت بیشتری پیدا کند و همچنین باعث افزایش قابلیت سختکاری فولاد می شود. |
کبالت | باعث می شود فولاد نسبت به گرما مقاومت بیشتری پیدا کند. |
گوگرد سرب کلسیم فسفر | باعث افزایش قابلیت ماشین کاری می شود. |
بحثی کوتاه در مورد فولاد های استاندارد
رایج ترین فولادها در صنعت مقدار کربن با درصد وزنی تقریبی چند هزارم درصد تا یک درصد است. علاوه بر این همه فولادها مقدارهای متفاوتی از عناصر دیگر به ویژه منگنز را دارند. منگنز به جز اینکه باعث کاهش اکسیژن ماده مذاب می شود توانایی کار فولاد گرم را هم زیاد می کند.
فولادها را می توان به روش ریخته یا شمش یا با گرم کردن دوباره با استفاده از روش های اکستروژن، فورج، نورد و یا به روش های دیگر تولید کرد و تغییر شکل داد. به همین علت در کاربردهای مهندسی تخصصی فولادهای شکل داده شده ای بیشتر مورد استفاده قرار میگیرد که دارای فرم، استحکام، کیفیت و دمای کاری متنوع تری باشند.
روش های جدا کردن ناخالصی در تولید فولاد
روش اول:
اغلب در دیواره داخلی کوره هایی که در تولید فولاد به کار می روند از آجرهایی استفاده می شود که این آجرها خودشان از مواد کمک ذوب ساخته شده اند. این پوشش از آجرها یک مقدار از اکسیدهای اضافی را که باید از مواد خارج شود جذب خود می کند که برای اینکه ناخالصی ها جدا شود از روش کوره باز استفاده می شود.
این کوره ها یک ظرف بشقاب مانند دارند که می توانند بین 100 تا 200 تن آهن مذاب را درون خود جا بدهند. در بالای این ظرف بشقاب مانند سقف مقعری وجود دارد که حرارت را بر روی سطح فلز مذاب انتشار می دهد و همچنین جریان بسیار شدیدی از اکسیژن را بر روی ماده مذاب عبور داده تا ناخالصی های موجود در ماده مذاب بسوزد. در این روش ناخالصی های موجود در ماده مذاب به وسیله انتقال گرما در مایع و عمل انتشار به سطح ماده مذاب رسیده و عمل تصفیه جندین ساعت زمان می برد. در این بین هم مقداری از آهن اکسید می شود که آن را جمع می کنند و به کوره بلند برگردانده می شود.
روش دوم:
در این روش هم از بعضی اصول که در روش قبل گفتیم استفاده می شود. به طوری که آهن ذوب شده را به همراه آهن قراضه و ماده کمک ذوب درون کوره های بشکه مانندی که گنجایش آنها 300 تن است می ریزند.
بعد از آن جریان شدیدی از اکسیژن خالص را با سرعت مافوق صوت بر روی فلز مذاب انتشار می دهند و با کج کردن و چرخاندن بشکه ها پی در پی سطح تازه ای از فلز مذاب در برابر اکسیژن قرار می گیرد و بعد دی اکسید کربن اکسایش ناخالصی ها با سرعت بیشتری انحام می شود. سپس فرآورده های گازی توده مواد مذاب را هم می زنند طوری که آهنی که در ته ظرف است رو بیاید.
درجه حرارت توده فلز مذاب بدون آنکه از حرارت خارجی استفاده شده باشد حدودا به دمای جوش آهن می رسد. در این دما واکنش ها بسیار سریع است و همه این مراحل در مدت زمان یک ساعت یا حتی کمتر انجام می شود و اغلب یک محصول با کیفیت و یکنواخت بدست می آید.
چند مورد از مهم ترین مجتمع های فولاد در ایران
نام کارخانه | روش تولید | ظرفیت تولید در هر سال |
مجتمع فولاد مبارکه اصفهان | احیای مستقیم | 8/8 میلیون تن |
مجتمع فولاد خوزستان | احیای مستقیم | 5 میلیون تن |
مجتمع ذوب آهن اصفهان | کوره بلند | 6/3 میلیون تن |
مجتمع فولاد خراسان | احیای مستقیم | 4/1 میلیون تن |
مجتمع معدنی صنعتی چادرملو | احیای مستقیم | 3/1 میلیون تن |
مجتمع ذوب آهن امیر کبیر اراک | کوره بلند | 1/1 میلیون تن |
مجتمع فولاد آذربایجان | احیای مستقیم | 8/0 میلیون تن |
مجتمع فولاد مبارکه اصفهان
می توان گفت شرکت فولاد مبارکه اصفهان بزرگ ترین واحد صنعتی فولادی در ایران است. این مجتمع در زمینی به متراژ 35 کیلو متر در نزدیکی شهر مبارکه و در 65 کیلومتری جنوب غربی اصفهان واقع شده است.
اگرچه استارت عملیات اجرایی مجتمع فولاد مبارکه در سال 1360 خورده شد ولی با شروع جنگ تحمیلی میان ایران و عراق و حملات هوایی جنگنده های عراقی ساختن آن حدود ده سال طول کشید.
بلاخره در سال 1370 با تجهیزات 500 هزار تنی و با ظرفیت حدود 2/4 میلیون تنی محصولات تولیدی آن به صورت تخت یعنی کلاف ورق گرم نورد شده و سرد نورد شده را راه اندازی کردند.
اولین کوره قوس الکتریکی در این مجتمع در مهر ماه سال 1370 نصب شد و آخرین خط نورد سرد هم در 23 دی سال 1371 نصب شد و خطوط تولید این مجتمع در همین تاریخ به وسیله رییس جمهور وقت افتتاح گردید.
یکی دیگر از طرح های توسعه ای این مجتمع فولادی, افتتاح بزرگ ترین و پیشرفته ترین واحد تولید آهن اسفنجی بوده است که عملیات اجرایی آن در 20 اردیبهشت 1387 شروع شد و در سال 1391 افتتاحیه آن انجام شد.
قابل ذکر است که مجتمع فولاد مبارکه اصفهان یکی از زیر مجموعه های سازمان توسعه و نوسازی معادن ایران است که توانایی آن را دارد که فعالیت های دیگری مثل فعالیت های فنی و سرمایه گذاری و بازرگانی را انجام بدهد.
خطوط تولیدی مجتمع فولاد مبارکه اصفهان عبارت است از:
- گندله سازی
- آهک پزی
- احیای مستقیم
- فولاد سازی
- ریخته گری پی در پی
- پرداخت وخنک کردن شمش
- نورد گرم و واحد تکمیل نورد گرم
- نورد سرد
- اسید شویی
- واحد تولید ورق گالوانیزه
- واحد تولیدی ورق قلع اندود
- و همچنین واحد تولیدی ورق رنگی
در انتها چند محصول مهم از تولیدات مجتمع فولاد مبارکه را به صورت کوتاه بیان می کنیم:
کلاف های اسید شویی، ورق کلاف و ورق گرم و سرد، کلاف نوار باریک و تختال هستند که این محصولات مورد نیاز صنایعی مثل صنایع لوازم خانگی، لوله سازی، خودرو سازی، مخزن های تحت فشار، تجهیزات فلزی سبک و سنگین هستند.
مجتمع ذوب آهن اصفهان
کارهای مربوط به ساخت پروژهی ذوب آهن بعد از اینکه دولت ایران و دولت شوروی سابق طی قرارداد در همکاری فنی و اقتصادی به توافق رسیدند و سپس در 23 دی ماه 1344 به تصویب مجلس رسید, انجام شد.
بر پایه این قرارداد مجتمع ذوب آهن ایران برای تهیه تجهیزات لازم در کارخانه و تجهیز کردن معدن های سنگ آهن، سنگ آهک و زغال سنگ با موسسهی تیاژپروم اکسپورت شوروی سابق قرار دادی را منعقد کرد.
پس از عقد قرارداد کارشناسان شوروی و ایرانی شروع به بررسی هایی کردند از جمله تامین آب، موقعیت محل از نظر زلزله، مواد اولیه، خطوط ارتباطی، انرژی الکترکی، عوامل اقتصادی، فنی و اجتماعی اصفهان و در انتها به این نتیجه رسیدند که کارخانه را در دشت طبس که در 45 کیلومتری جنوب غربی اصفهان است احداث کنند.
مراحل احداث مجتمع ذوب آهن در اصفهان
عملیات اجرای ساخت واحد های مجتمع در سال 1346 با ساختن کارگاه های کک سازی، اگلو مراسیون و کوره بلند با ظرفیت تولیدی 550 هزار تن فولاد شروع شد و در سال 1350 به بهره برداری رسید.
سپس یکسال بعد در سال 1351 فاز دوم توسعه با هدف رسیدن به ظرفیت یک میلیون و 900 هزار تن فولاد در سال, با احداث واحد کوره بلند، بهره بردای از مجتمع چدن، توسعه بخش های مختلف الگلومراسیون، کک سازی، فولاد سازی و مهندسی نورد آغاز شد.
بعد از آن در سال 1357 هم عملیات ساختمان کمپلکس چدن به پایان رسید. سپس بعد از پیروزی انقلاب اسلامی و شروع جنگ تحمیلی عراق با ایران روند پیشرفت و توسعه در صنایع به خصوص صنعت فولاد کشور با کندی پیش رفت ولی بعد از جنگ مجتمع ذوب آهن با به کار بردن امکانات و تلاش و زحمت متخصصان ایرانی توانست تولیدات خود را به مرز 2 میلیون تن برساند.
مطالب پیشنهادی
- تسمه آهنی چیست؟
- تسمه نوردی
- با انواع نبشی و کاربردهای آن بیشتر آشنا شوید
- آشنایی با فرآیند تولید تیرآهن + معرفی تیرآهن لانه زنبوری
- چگونگی محاسبه قیمت انواع میلگرد
- پروفیل چگونه تولید میشود؟