پس از استخراج آهن و تولید فولاد خام, اولین محصولی که به دست می آید تا در موارد مختلف مورد استفاده قرار بگیرد “شمش فولادی” است. این شمش ها معمولا به صورت جامد و در ابعاد مختلف و قابل حمل تولید می شوند.
در ادامه قصد داریم اطلاعاتی در مورد شمش های فولادی, انواع آنها و … در اختیار شما قرار دهیم. با ما تا پایان همراه باشید.
شمش فولادی چیست؟
شمش فولادی یا Steel Ingot ماده اولیه برای صنایع فولادسازی است که حاصل از انجماد فلز مذاب در قالب های مخصوص است. آهن و سایر مواد آلیاژی با کمک سنگ آهن و زغال سنگ در کوره های القایی یا قوس الکتریکی ذوب شده و سپس در داخل قالبی به شکل دلخواه ریخته گری می شوند.
در واقع شمش یک محصول فولادی و ریخته گری است و از مهم ترین مواد اولیه در صنایع تولید مقاطع فولادی به حساب می آید.
شکل ظاهری شمش فولادی معمولا به صورت مکعب, میله,صفحه یا ورق است.
تمامی فلزات از جمله طلا, نقره, مس, آلومینیوم و فولاد برای هر گونه تغییر شکل و پردازش های مورد نظر اول به صورت شمش در می آیند. وزن تقریبی شمش ها میتواند از 300 کیلوگرم تا 9 تن باشد.
تولید اولین شمش فولادی
گستردگی استفاده از شمش ها مخصوصا شمش فولادی این روزها بر کسی پوشیده نیست. اسناد تاریخی موجود نشان می دهند که اولین شمش در دوران هخامنشیان ساخته شده. اما تولید شمش فقط به این دوران مربوط نبوده و در جهان از شمش های طلا و نقره به عنوان پول و برای تبادل استفاده می شده.
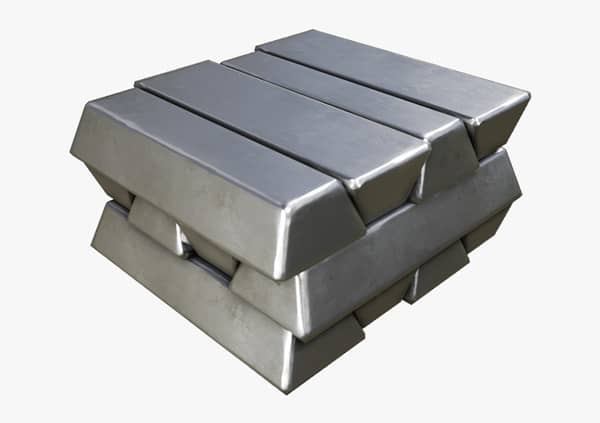
برای اثبات این حرف می توان به تصاویر بانک های قدیمی اشاره کرد که معمولا در آن هرم هایی به نمایش در آمده است که این هرم ها حاصل روی هم قرار گرفتن شمش های طلا بوده است.
برای تولید محصولاتی مانند میلگرد, تیرآهن, ورق فلزی و … از شمش فولادی استفاده می شود. به همین دلیل می توان گفت که صنعت فولاد وابستگی مستقیمی به شمش فولادی دارد.
انواع شمش فولادی
شمش ها انواع مختلفی دارند و از هر کدام از آنها برای تولید مقطع خاصی استفاده می شود؛
شمش (ingot)
به این شمش, “شمش دستی” هم گفته می شود که دارای سطحی ذوزنقه شکل است. دلیل اینکه این شمش را در قالب هایی به این شکل تولید می کنند این است که حمل و نقل و جابه جایی آنها راحت تر باشد. طول هر شاخه آن نیز حدود 2 متر است.
بیلت (billet)
به بیلت ها “شمشال” نیز گفته می شود و از پر طرفدارترین محصولات به حساب می آید. این محصول میانی نورد فولاد به روش ریخته گری مدام یا CCM تولید می شود که کوتاه شده عبارت Continue Casting Machine است.
طول شمش بیلت از شمش های دستی بیشتر است و سطح مقطع آن به صورت دایره ای یا مربعی با قطر حداکثر 15 سانتی متر می باشد.
از این شمش بیشتر برای تولید میلگرد و سیم استفاده می شود.
بلوم (bloom)
این نوع شمش به “شمشه” یا “شمش فابریک” نیز معروف است. در واقع ریخته گری و روش تولید این شمش به سبک تولید بیلت است اما قطر سطح مقطع بلوم بیشتر از 15 سانتی متر است.
از این شمش بیشتر برای تولید ریل, گل میخ, تیرآهن, ناودانی و قوطی استفاده می شود.
اسلب (slab)
به اسلب “سلب” یا “تختال” نیز گفته می شود که با ریخته گری مدام یا نورد گرم سایر شمش ها به دست می آید.
این شمش دارای سطح مقطع مستطیلی با طول معمول 12 متر, عرض 25/1 متر و ضخامت 230 میلیمتر است.
معمولا از اسلب ها برای ساخت ورق فولادی با نورد سرد یا گرم استفاده می شود.
در حالت کلی آنچه در تولید شمش های با کیفیت موثر است, مواد اولیه, شیوه ذوب و ریخته گری است.
تفاوت انواع شمش های معرفی شده در چیست؟
تا اینجا با انواع شمش ها و کاربرد آنها تا حدودی آشنا شدیم. و متوجه شدیم که تمامی شمش ها با همه تفاوت هایی که با هم دارند از سنگ آهن به وجود آمده اند و درصد قابل توجهی از کیفیت آنها به کیفیت سنگ آهن اولیه بستگی دارد.
تفاوت اصلی انواع شمش ها در سطح مقطع و اندازه آنهاست.
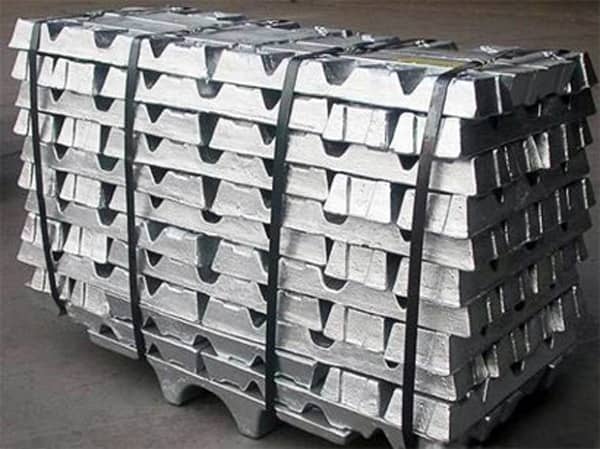
تولید کنندگان شمش فولادی
کارخانه های مختلف ایرانی و خارجی وجود دارند که به تولید انواع شمش می پردازند. از کارخانه های داخلی تولید کننده این محصول می توان به شرکت های ذوب آهن اصفهان، فولاد مبارکه اصفهان، فولاد خوزستان، فولاد خراسان، فولاد صنعت بناب، فولاد سیرجان و … اشاره کرد.
در حقیقت قاره آسیا قطب صنعتی ساخت شمش های فولادی است و در بین کشورهای تولید کننده این محصول چین رتبه اول را در جهان دارد.
به چه روش هایی شمش فولادی تولید می شود؟
معمولا شمش فولادی به سه روش کلی تولید می شود؛
1.تولید شمش فولادی با استفاده از کوره بلند
یکی از معمول ترین روش ها برای تولید شمش فولادی استفاده از روش کوره بلند یا Blast Furnace است.
در این روش سنگ آهن همراه با ضایعات آهن وارد کوره شده و با استفاده از اکسیژن ذوب می شود. فرآیند ذوب مواد به این روش را “اکسیژن بازی” می گویند. در این فرآیند اکسیژن توسط دو لوله نیزهای شکل وارد کوره میشود که سرعت آن دو برابر سرعت صوت است. بعد از این مرحله گرمادهی شروع می شود.
یکی از محصولات تولید شده به این روش “اسلب” است که پیشتر به معرفی آن پرداختیم.
در این روش اضافه کردن اکسیژن باعث اکسیداسیون میشود که در نتیجه آن ناخالصی های موجود از بین می روند.
در حین فرآنید برای جذب بیشتر ناخالصیها، آهک به کوره اضافه میشود. آهک و ناخالصیها با یکدیگر واکنش داده و تولید سرباره میکنند.
در نهایت فولاد تولید شده در روش کوره باز اکسیژنی، از حفره کنورتور خارج میشود.
مقاله پیشنهادی برای مطالعه بیشتر؛ ضایعات آهن, کاربردها و اطلاع از قیمت به روز آن
برخی از مزایای این روش؛
- در این روش ناخالصی ها به طور چشمگیری جدا می شوند.
- امکان تولید با حجم بالا نیز با استفاده از این روش وجود دارد.
در کنار مزایا به برخی از معایب آن باید بپردازیم؛
- ضایعات تولید شده به این روش بسیار زیاد است.
- فولاد تولیدی خیلی انعطاف قابل توجهی ندارد.
- گازهای تولیدی در این روش آلایندههای قوی محسوب میشوند و برای محیط زیست مناسب نیستند.
2.تولید شمش فولادی با استفاده از کوره قوس الکتریکی (EAF)
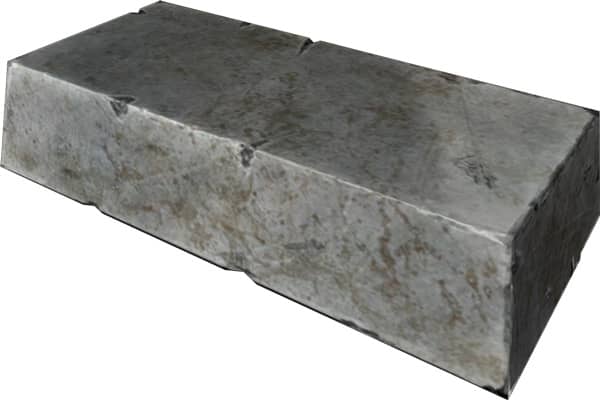
فولاد تولید شده به این روش با استفاده از ضایعات فولادی ساخته می شود. این ضایعات را می توان در سه دسته زیر طبقه بندی کرد؛
- ضایعات خانگی
- ضایعات صنعتی
- ضایعات کهنه
کوره قوس الکتریکی را می توان مانند یک حمام بزرگ اما کم عمق در نظر گرفت. الکترودهای کربنی در بالای این حمام قرار گرفته اند.
برای شروع فرآیند, ضایعات فولادی با جرثقیل داخل کوره قرار می گیرند. با جایگذاری این ضایعات, الکترود به سمت پایین هدایت می شود. همزمان با این کار جریان الکتریکی نیز برقرار می شود و باعث ذوب شدن فلزات می شود.
در واقع دمای الکترود در این فرآیند 4100 درجه سانتی گراد است که این دمای بالا باعث ذوب شدن فلزات می شود.
مزیت های کوره قوس الکتریکی؛
- به دلیل انعطاف بالای این فرآیند می توان برای تولید انواع شمش ها از آن استفاده کرد.
- دمای فولاد مذاب کاملا تحت کنترل است.
- کیفیت و ضایعات فولاد در کوره قوس الکتریکی از کوره بلند بهتر است.
معایب کوره قوس الکتریکی:
- در این فرآیند کیفیت محصول نهایی وابسته به ضایعات در دسترس است.
- هزینه انرژی به دلیل استفاده از برق و مدتزمان بیشتر ذوب فولاد بسیار بالا است.
- ناخالصی بیشتر وارد فولاد شده و کیفیت فولاد کم میشود.
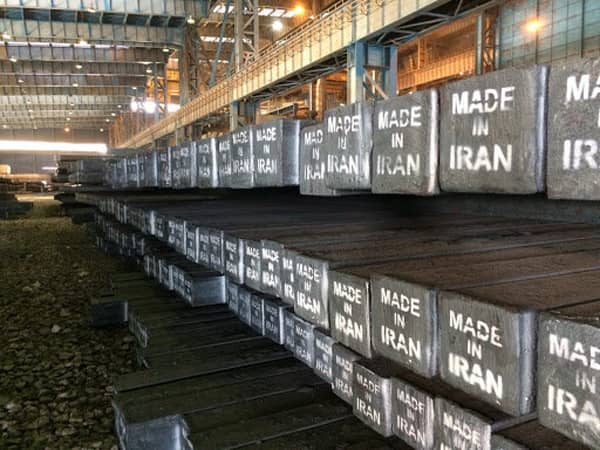
3.تولید شمش فولادی با استفاده از کوره ذوب القایی (IMF)
در این روش میدان مغناطیسی باعث ذوب شدن ضایعات وارد شده می شود و این یکی از تفاوت های اساسی با سایر روش هاست.
یک سیمپیچ القایی که به دور کوره پیچیده شده است در هنگام وجود جریان الکتریسیته با فرکانس بالا میدان مغناطیسی ایجاد کرده و گرما تولید میکند. سپس دمای بالا به داخل کوره منتقل شده و ذوب فلزات را موجب میشود.
مزیت استفاده از این روش؛
- فرآیند عملکردی این کوره بسیار ساده و راحت است.
- در این روش هیچگونه آلودگی صوتی وجود ندارد. در صورتی در کوره قوس الکتریکی صدای زیادی تولید می شود.
- راندمان حرارتی در این کوره بسیار بالا است.
عیب هایی که می توان برای کوره القایی در نظر گرفت؛
- چون برای عملکرد کوره به فرکانس بالای جریان الکتریکی نیاز است، بنابراین قیمت کوره بسیار بالا است.
- از آنجا که سطح فوقانی مذاب دارای تلاطم و دمای آن سرد است، امکان تولید سرباره نیست.
قیمت روز شمش فولادی
از آنجایی که قیمت مقاطع فولادی وابسته به موارد مختلفی از جمله نوسان ارز, دلار, مسائل و شرایط اجتماعی و سیاسی و … می باشد, به طور مدام در حال تغییر است.
برای اطلاع از قیمت انواع شمش فولادی می توانید با کارشناسان آهن جردن تماس بگیرید. کارشناسان ضمن اعلام قیمت های به روز می توانند شما را برای یک خرید مطمئن و بی دردسر راهنمایی کنند و تا پایان در کنار شما باشند.